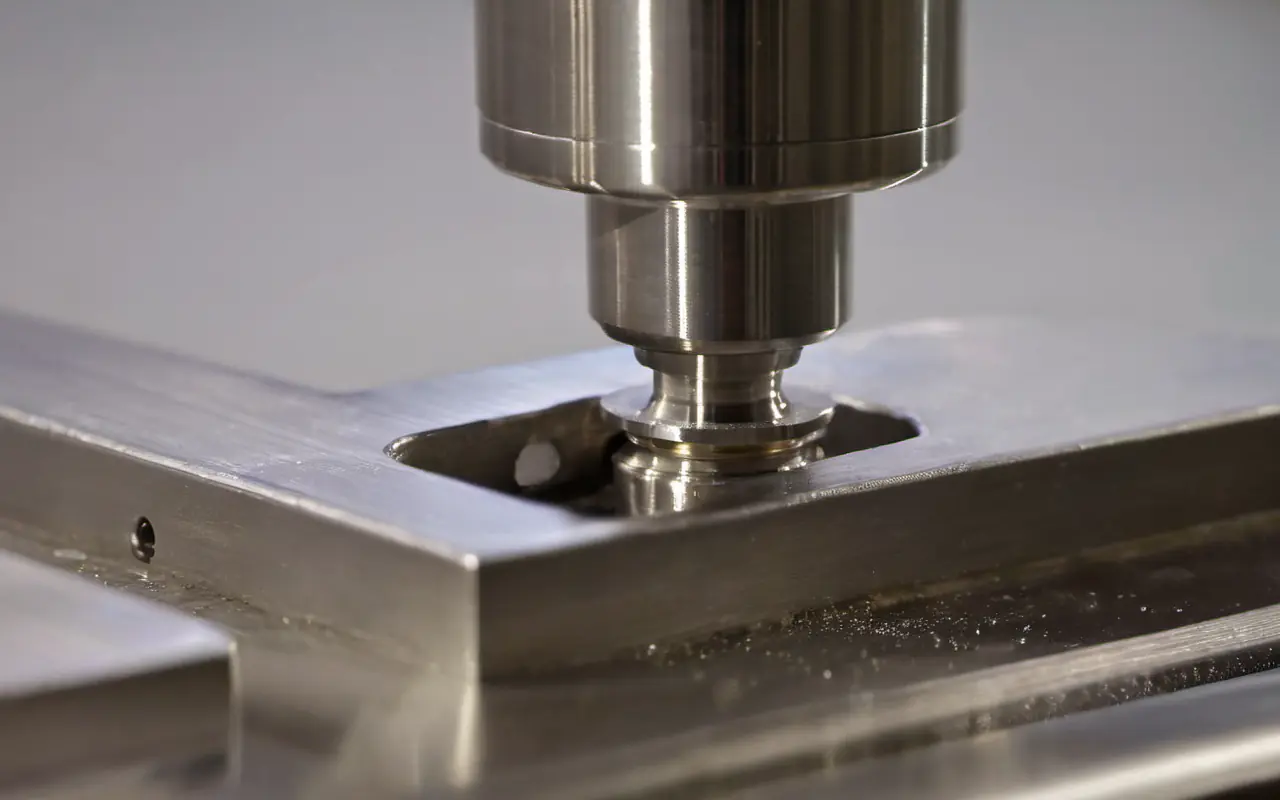
Dobrze już znana i ceniona na rynku technologia CNC (Computer Numerical Control) umożliwiająca komputerowe sterowanie maszynami do precyzyjnej obróbki materiałów to obecnie standard. Współczesne systemy CNC znajdują zastosowanie w wielu sektorach przemysłu, rewolucjonizując procesy produkcyjne. Wpływ tej technologii na branże takie jak lotnictwo, motoryzacja czy medycyna jest nieoceniony – pozwala na wytwarzanie detali o wysokim stopniu złożoności i dokładności. Jednak wciąż nie wszyscy zdają sobie sprawę z tego, na czym ona dokładnie polega, a także jak wygląda proces obróbki elementów z zastosowaniem komputerowej automatyzacji. W tym wpisie szczegółowo omówimy, czym jest obróbka CNC, jak przebiega, jakie ma zastosowania, a także wskażemy zalety i ograniczenia tej technologii. Wejdź z nami do świata automatyzacji obróbki – zapraszamy do lektury!
Z tego wpisu dowiesz się:
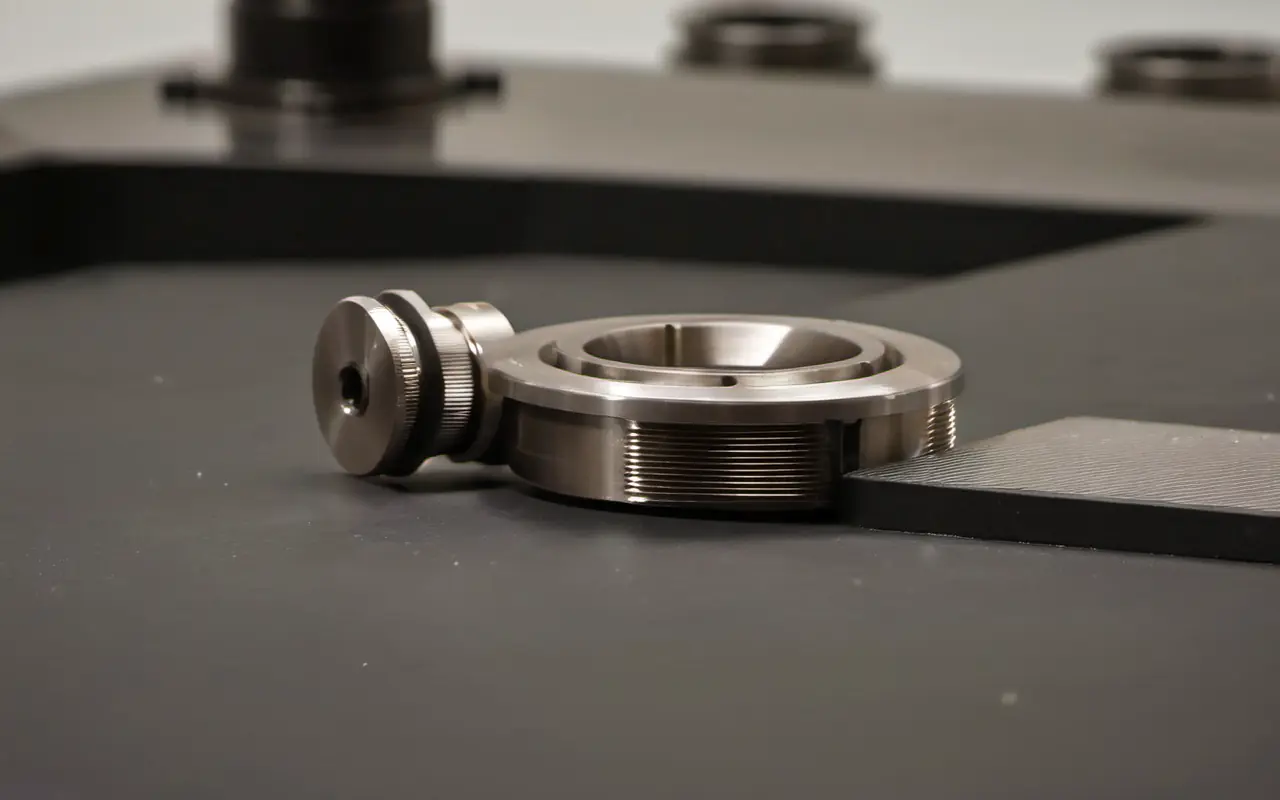
Czym jest obróbka CNC?
Zanim przejdziemy do klasyfikacji tego procesu, przypomnijmy, czym w zasadzie jest obróbka CNC. Szczegółowo mówiąc, to proces technologiczny polegający na kształtowaniu materiałów przy użyciu maszyn sterowanych komputerowo. W przeciwieństwie do tradycyjnych metod obróbki eliminuje konieczność ręcznego prowadzenia narzędzi po konkretnym obszarze – minimalizuje to błędy i zwiększa jednocześnie powtarzalność produkcji. System CNC składa się z kilku istotnych elementów. Jakich?
Oprogramowanie CAD/CAM | Maszyny i narzędzia | Sterowniki komputerowe |
---|---|---|
Umożliwia tworzenie modeli 3D i generowanie kodów sterujących maszynami.
Zmniejsza koszty siły roboczej, eliminując potrzebę ręcznego sporządzania projektów, które mogą być błędne i niedopracowane. |
Obejmują tokarki, frezarki, centra obróbcze i wycinarki laserowe.
Umożliwiają przeprowadzenie skomplikowanych procesów obróbczych, po wcześniejszym zaplanowaniu działań z oprogramowaniem CAD/CAM. |
Realizują zaprogramowane ruchy narzędzi, monitorują cały proces obróbczy.
Współpracują z maszynami i narzędziami, a tym samym działają zgodnie z wytycznymi wskazanymi w komputerowym oprogramowaniu. |
Technologia CNC pozwala na obróbkę różnorodnych materiałów, takich jak:
- metale (stal, aluminium, miedź),
- tworzywa sztuczne,
- kompozyty, w tym laminaty HPL.
CNC znajduje zastosowanie zarówno w produkcji elementów konstrukcyjnych, jak i precyzyjnych części mechanicznych.
Jak przebiega obróbka CNC?
Proces obróbki CNC to złożone działania, które muszą przebiegać w kilku etapach. Ważne jest, że każdy z nich wynika bezpośrednio z innego, gwarantując ostatecznie odpowiednio obrobiony produkt, zgodny ze wszystkimi wskazanymi wytycznymi. Przeanalizujmy teraz krok po kroku działania skupione wokół technologii CNC.
Proces projektowania
Inżynierowie odpowiedzialni za przygotowanie projektu tworzą model detalu w oprogramowaniu CAD, określając wszystkie wymiary, tolerancje oraz właściwości materiału. Na tej podstawie przygotowuje się plan obróbki w systemie CAM.
Programowanie działań
Obejmuje tworzenie i wprowadzanie kodów sterujących, które definiują ruchy narzędzi, parametry pracy oraz kolejność wykonywanych operacji. Ten proces wymaga nie tylko zaawansowanej wiedzy technicznej, ale również znajomości wspomnianego oprogramowania CAD/CAM oraz języka programowania maszyn, najczęściej G-code.
Obróbka właściwa
Obróbka właściwa to etap, w którym maszyna CNC przystępuje do realizacji wcześniej zaprogramowanego zadania. Proces rozpoczyna się od zamocowania półfabrykatu na stole roboczym lub w uchwycie, następnie uruchamiany jest zaprogramowany cykl obróbki, podczas którego maszyna automatycznie kształtuje materiał zgodnie z wytycznymi zawartymi w kodzie sterującym. W zależności od rodzaju maszyny i zastosowanego narzędzia, proces ten może obejmować różne operacje, takie jak toczenie, frezowanie, wiercenie, gwintowanie czy wycinanie.
Kontrola jakości
Gotowy detal podlega pomiarom wymiarowym i analizie powierzchni w celu sprawdzenia zgodności z projektem. Proces ten obejmuje także ocenę parametrów powierzchni, takich jak chropowatość czy geometria detalu. Precyzyjna weryfikacja jest szczególnie istotna w branżach wymagających wysokiej dokładności, takich jak lotnictwo, medycyna czy motoryzacja.
Z punktu widzenia poprawności procesów CNC istotne stają się także symulacje obróbki. Czym są? To działania polegające na kontroli w oprogramowaniu CAM pozwalające przewidzieć potencjalne problemy i zoptymalizować proces jeszcze przed rozpoczęciem pracy na maszynie.
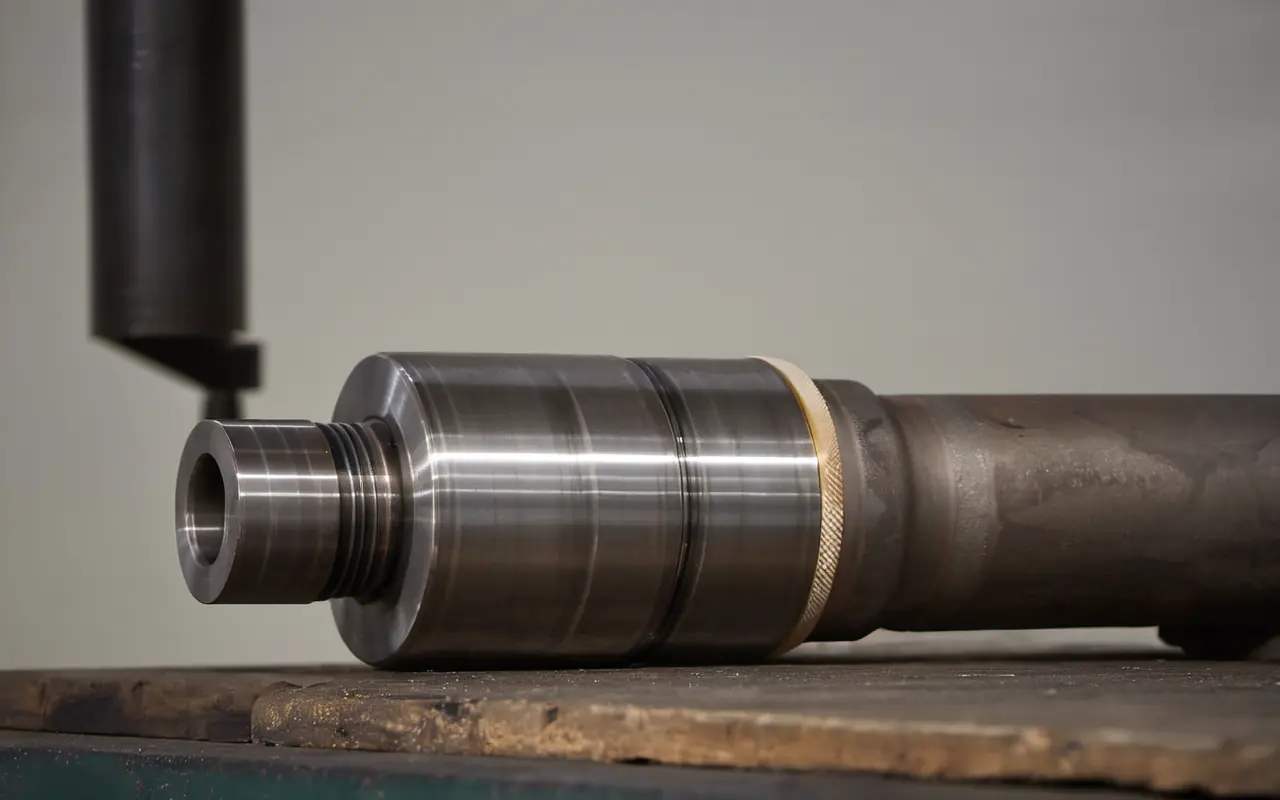
Kiedy warto zastosować obróbkę CNC?
Jak już wspomnieliśmy w tym wpisie, współcześnie obróbka CNC znajduje zastosowanie w naprawdę wielu obszarach produkcyjnych, zarówno w tworzeniu seryjnym, jak i jednostkowym. W produkcji masowej technologia ta gwarantuje bowiem wysoką powtarzalność, umożliwiając szybkie wygenerowanie dużej liczby identycznych elementów o jednolitej jakości. Z kolei w prototypowaniu pozwala na precyzyjne wykonanie skomplikowanych detali, które wymagają dokładnego odwzorowania projektu. Technologia ta znajduje również zastosowanie w produkcji narzędzi i komponentów wymagających wysokiej precyzji, takich jak części maszyn, elementy konstrukcyjne czy nawet precyzyjne detale medyczne. Dzięki zaawansowaniu systemów CNC możliwa staje się szybka zmiana parametrów produkcji – doceniają to zwłaszcza firmy realizujące różnorodne zlecenia w krótkim czasie, dotyczące np. elementów sezonowych.
Zalety i wady obróbki CNC
Chociaż obróbka CNC jest zdecydowanym ułatwieniem procesów produkcyjnych – umożliwia bowiem osiągnięcie wydajności niedostępnej w tradycyjnych metodach obróbki, to jednak nie pozostaje technologią bez wad. Prześledźmy teraz zarówno pozytywne, jak i negatywne aspekty obróbki skrawaniem, które jasno wskazują, czy jest to rozwiązanie warte uwagi.
Zalety
- Precyzja i powtarzalność – automatyzacja CNC pozwala na wykonanie detali o złożonych kształtach z dokładnością rzędu mikrometrów. Każdy element jest identyczny, a ma to nadrzędne znaczenie w produkcji seryjnej.
- Skrócenie czasu produkcji – przestawienie procesów obróbki z ręcznego na mechaniczne umożliwia szybsze wykonanie dużej liczby elementów, eliminując przy tym przestoje wynikające z tradycyjnej obsługi maszyn.
- Elastyczność technologiczna – możliwość zaprogramowania maszyn pozwala na realizację różnorodnych zleceń bez potrzeby zmiany całego parku maszynowego. Ma to także znaczenie w kwestii finansowej, gdyż nie trzeba inwestować w kolejne skomplikowane urządzenia produkcyjne.
- Automatyzacja – jako że maszyny CNC mogą pracować bez przerwy, zwiększa się efektywność produkcji i możliwa staje się realizacja zadań w trybie ciągłym. Wystarczy jedynie etapowa kontrola, czy system pracuje prawidłowo, jednak jest ona wyłącznie zalecana w celach zyskania pewności co do powodzenia projektu.
Wady
- Wysokie koszty inwestycyjne – zakup maszyn, uzyskanie legalnego oprogramowania oraz szkolenie personelu w zakresie planowania prac związanych z CNC generują duże kwoty, choć trzeba wskazać, że są to jedynie koszty początkowe.
- Konieczność posiadania kompetencji – obsługa maszyn CNC oraz zaawansowane programowanie wymagają odpowiedniego doświadczenia i wiedzy technicznej, a to zwiększa zapotrzebowanie na wykwalifikowanych pracowników.
W zestawieniu zalet vs. wad jasno widać, że korzyści przemawiających za wykorzystaniem tej technologii jest znacznie więcej. Wiele firm oraz przedsiębiorstw produkcyjnych zdecydowało się już na ten krok. Pora na Ciebie!
Nie ma co ukrywać, że CNC to technologia, która zmienia sposób produkcji, gwarantując przy tym precyzję ruchów, efektywność prac i elastyczność w dostosowaniu działań do danej branży. Jej obecność w przemyśle pozwala na realizację nawet najbardziej wymagających projektów! Inwestycja w maszyny CNC to zatem krok w stronę nowoczesności połączonej z innowacyjnością na rynku, która umożliwia firmom osiąganie przewagi konkurencyjnej na dynamicznie rozwijającym się obszarze produkcyjnym.