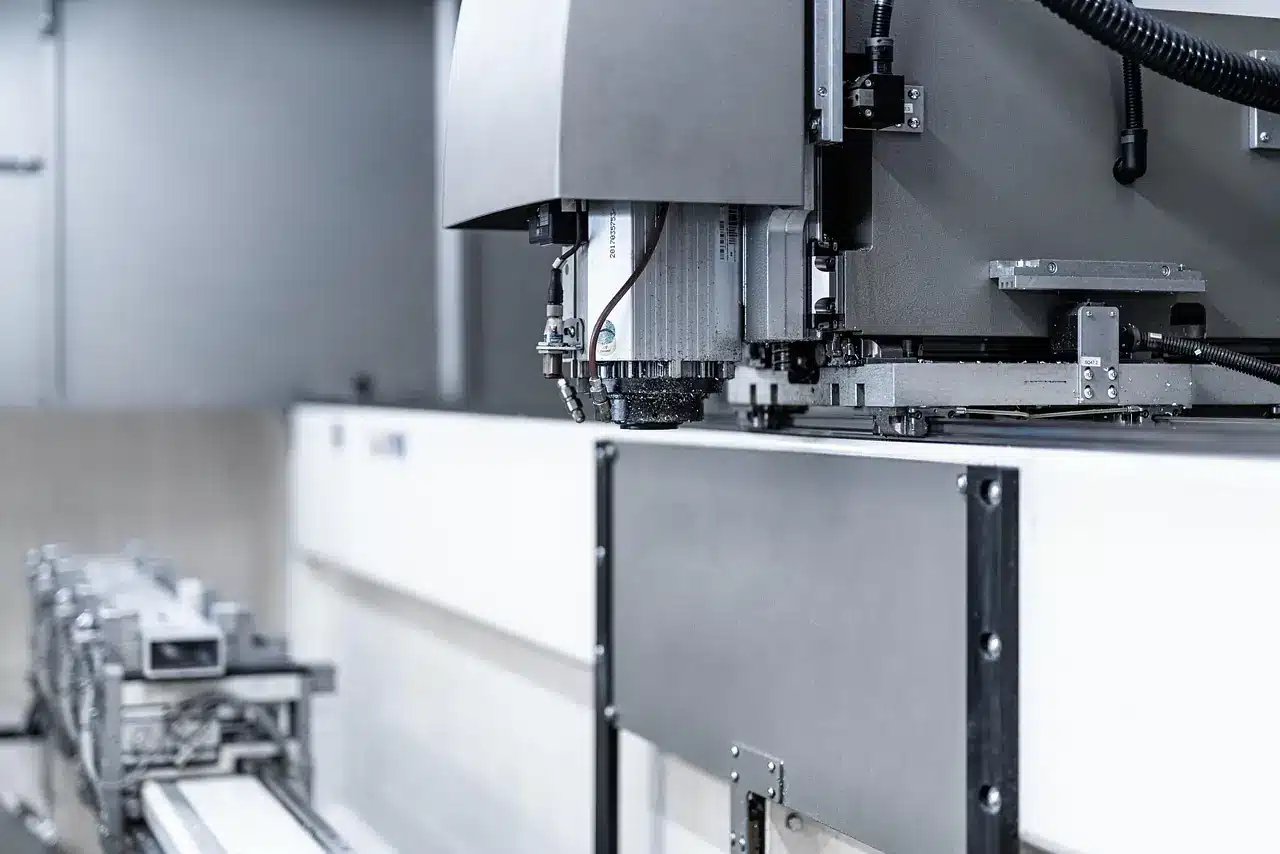
Wiertarki do głębokich otworów są niezbędnym narzędziem w wielu branżach przemysłowych, w których wymagana jest precyzyjna obróbka materiałów o dużej twardości. Wykorzystywane są do wiercenia otworów o dużej głębokości w stosunku do średnicy, a to z kolei stawia przed nimi specyficzne wymagania dotyczące konstrukcji oraz technologii obróbczej. Na rynku dostępne są różne typy maszyn, przeznaczonych m.in. do wykonywania do głębokich otworów, wiertarko-wytaczarki czy wytaczarki poziome. Wszystkie z tych urządzeń różnią się przeznaczeniem oraz możliwościami technologicznymi, a ich wybór zależy od specyfiki produkcji i rodzaju obrabianych materiałów. Zastanawiasz się, jakie urządzenie będzie najlepsze w Twoim przypadku? W tym artykule omówimy główne cechy tych maszyn, ich zastosowania oraz kryteria wyboru odpowiedniego urządzenia do produkcji. Zapraszamy do lektury!
Z tego wpisu dowiesz się:
Czym jest wiertarka do głębokich otworów?
Wiertarka do głębokich otworów to maszyna służąca do wykonywania otworów o dużej głębokości w stosunku do ich średnicy, z zachowaniem wysokiej precyzji. Charakteryzuje się specjalistycznym systemem chłodzenia, umożliwiającym skuteczne odprowadzanie ciepła powstającego podczas wiercenia. W zależności od typu możliwe jest stosowanie różnych narzędzi skrawających, takich jak wiertła o dużej długości czy wiertła stożkowe, które pozwalają na wiercenie głębokich otworów o małej średnicy. Wiertarka do głębokich otworów znajduje zastosowanie głównie w przemyśle motoryzacyjnym, przemysłowym czy energetycznym, ponieważ to właśnie w takich przedsiębiorstwach wykonywane są precyzyjne otwory w materiałach twardych, takich jak stal nierdzewna czy tytan. Dzięki dużej stabilności maszyny i zaawansowanemu systemowi sterowania wiertarki te gwarantują powtarzalność i wysoką jakość wykonania – mogą być przez to zastosowane w produkcji elementów silnikowych, turbin bądź innych skomplikowanych części, wymagających doskonałej precyzji.
Wiertarko-wytaczarka – połączenie kilku funkcji w jednym urządzeniu
Wiertarko-wytaczarka jest z kolei nieco bardziej zaawansowanym urządzeniem, gdyż łączy w sobie funkcje wiertarki oraz wytaczarki, umożliwiając – jak sama nazwa wskazuje – jednoczesne wiercenie i wytaczanie w jednym cyklu obróbczych. Dzięki tej kombinacji maszyna staje się wyjątkowo uniwersalnym narzędziem w obróbce precyzyjnej, szczególnie gdy wymagane jest przeprowadzenie kilku operacji na jednym detalu. Wiertarko-wytaczarka umożliwia wiercenie otworów o dużej głębokości, a następnie ich precyzyjne wytaczanie, przekładając się na uzyskanie dokładnych wymiarów i odpowiedniej jakości powierzchni. Takie rozwiązanie znacząco zwiększa wydajność produkcji, redukując czas potrzebny na wykonanie poszczególnych etapów obróbki. Wiertarko-wytaczarki są szczególnie przydatne w produkcji detali o złożonej geometrii, takich jak elementy do form wtryskowych, matryc czy części precyzyjnych w przemyśle lotniczym i motoryzacyjnym, a dzięki zaawansowanemu sterowaniu numerycznemu (CNC) charakteryzują się dużą dokładnością idącą w parze z powtarzalnością obróbki.
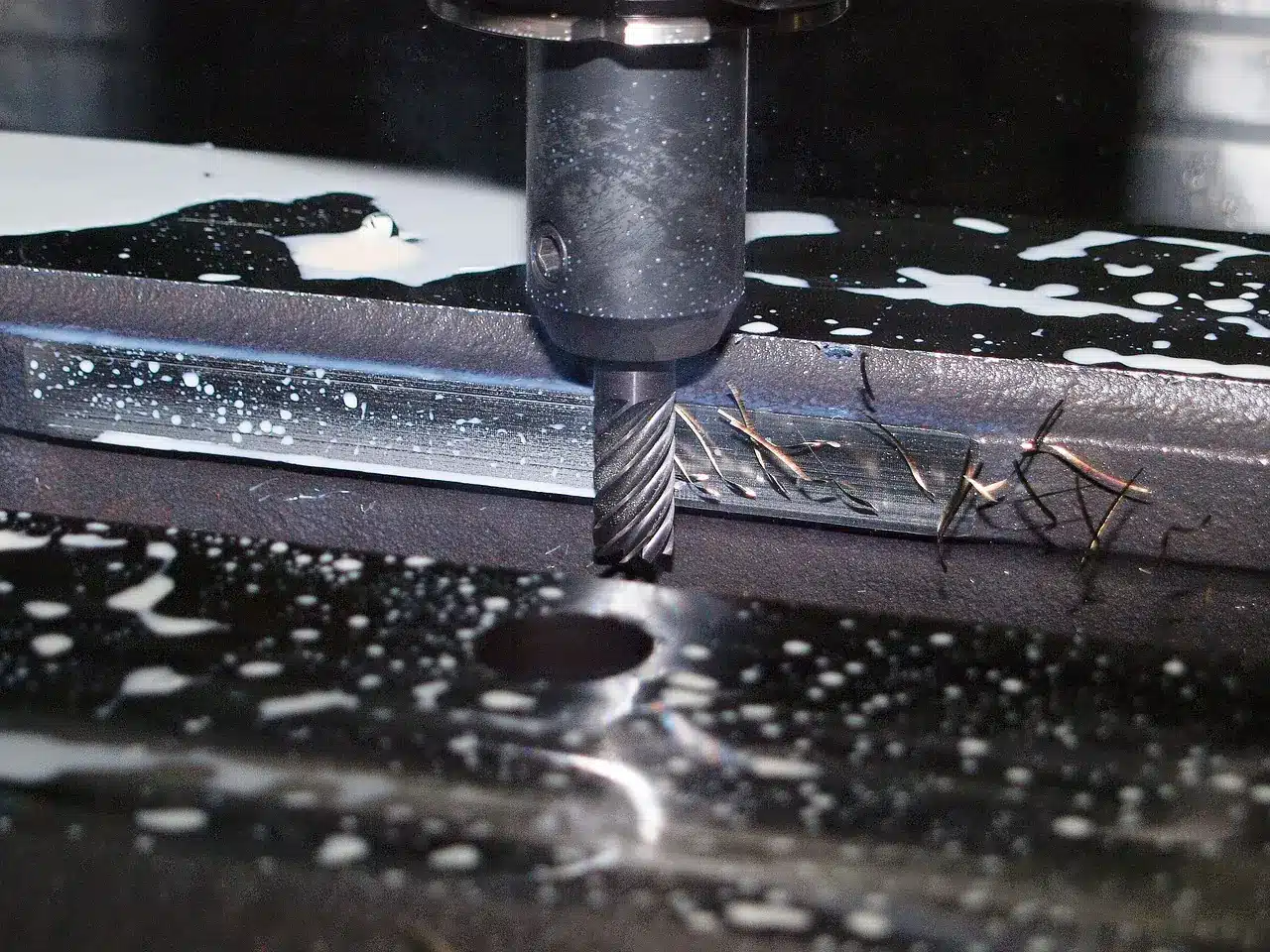
Wytaczarki poziome. Kiedy warto je wybrać?
Pozostaje nam przedstawienie ostatniego typu urządzeń – są nim wytaczarki poziome, wykorzystywane głównie w obróbce dużych detali, podczas której liczą się wysoka stabilność oraz precyzyjne wytaczanie. Wytaczarki poziome posiadają poziomą oś narzędzia skrawającego, jaka pozwala na obróbkę dużych elementów w sposób stabilny, z zachowaniem wysokiej dokładności. Są wykorzystywane w produkcji elementów wymagających wykonania dużych otworów o precyzyjnych wymiarach, jak na przykład korpusy silników, matryce czy części do maszyn przemysłowych. Urządzenia te są również często stosowane tam, gdzie detale mają większe wymiary, a wymagania dotyczące precyzji zdecydowanie przewyższają podstawowe wytyczne. Zaletą wytaczarek poziomych jest również ich zdolność do pracy z materiałami o różnej twardości, w tym stalami nierdzewnymi czy stopami tytanu, a to czyni je wszechstronnym narzędziem w produkcji przemysłowej.
Jak wybrać odpowiednią maszynę do głębokich otworów?
Znasz już wszystkie typy maszyn przeznaczonych do wykonywania głębokich otworów. Ale który będzie optymalny dla Twojego przedsiębiorstwa? Otóż wybór odpowiedniego urządzenia zależy od wielu czynników, takich jak rodzaj materiału, głębokość otworu czy wymagana precyzja. W przypadku obróbki głębokich otworów wiertarka do głębokich otworów będzie najlepszym wyborem, zwłaszcza gdy konieczne jest wykonanie otworów o dużych proporcjach średnicy do głębokości. Jeśli jednak produkcja wymaga bardziej złożonych operacji, takich jak wiercenie i wytaczanie w jednym cyklu, wiertarko-wytaczarka może okazać się korzystniejszym rozwiązaniem. Z kolei gdy obróbka dotyczy dużych detali, wymagających maksymalnej stabilności i precyzji, warto rozważyć wytaczarkę poziomą – sprawdzi się ona zwłaszcza w produkcji dużych elementów o wymagających geometriach.
Na co zwrócić uwagę przy wyborze maszyny?
- Rodzaj materiału i twardość obrabianego detalu,
- wymagana precyzja otworu oraz jakość powierzchni,
- typ produkcji (seryjna czy jednostkowa),
- wydajność maszyny i możliwość integracji z innymi systemami obróbczymi.
Decyzja o wyborze odpowiedniej maszyny do głębokich otworów ma duży wpływ na sukces produkcji wymagającej precyzyjnych wierceń. Wiertarka do głębokich otworów, wiertarko-wytaczarka oraz maszyna pozioma różnią się bowiem zakresem prac i przeznaczeniem, a ich odpowiednie dopasowanie może znacząco wpłynąć na jakość wraz z efektywnością produkcji. Każda z tych maszyn posiada nieco inne zalety, idealnie dopasowane do specyficznych zadań, takich jak wiercenie w twardych materiałach czy obróbka dużych detali. Przy wyborze urządzenia uwzględnij więc takie czynniki jak tworzywo, głębokość otworu, precyzja wykonania i wydajność. Odpowiednia technologia może znacznie przyspieszyć proces produkcyjny, a zarazem poprawić jakość finalnych produktów – jeśli masz jednak wątpliwości, polecamy skonsultować się z naszymi ekspertami! Pomożemy Ci dopasować najbardziej odpowiednie rozwiązanie do specyficznych potrzeb produkcji.